- HOME
- スピードと品質で実現“精鮮部品”工程
- この製品はこうして生まれた vol.01
スピードと品質を支える生産工程
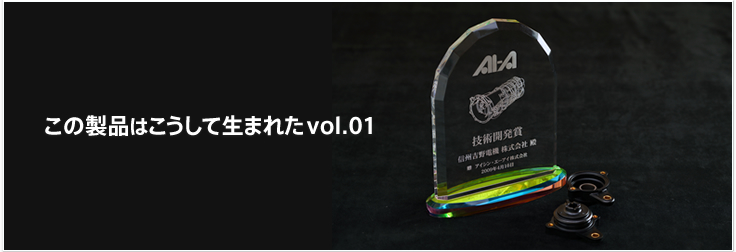
2007年2月‐それは突然舞い込んだ
京都議定書の発行によって温室効果ガス排出量の削減(2008年~2012年の間に1990年時より少なくとも5%の削減)が定められてからというもの、自動車業界でも環境問題には真剣に取り組んでいた。CO2の削減とコスト削減に向けた軽量化は大きな課題のひとつとなっていた。
そんなある日、車のトランスミッションに使用している部品についての見積もり依頼が舞い込んだ。アルミダイキャストで製造している部品を軽量化するため「樹脂化できないか」との内容である。
取引先との窓口となる「営業部」を持たない信州吉野電機株式会社は、いわば社員全員が技術者であり会社のカオでもある営業部員がアルミダイキャスト品の樹脂化の兼務をする。だから、即答とまではいかないが、依頼を聞いた各部署のエキスパートたちは集まった瞬間からイメージの中では製品が完成する。
その後はチームで膝を交え、知恵を絞り、フィードバックし、試行錯誤を繰り返し、そして「樹脂化」を成功させた。コストはもちろんのこと重量においては12.01gの減量。その上、製品開発に挑む真摯な姿勢と納期対応などを高く評価され、顧客側から開発費用の折半を提案され、さらには「技術開発賞」という名誉ある表彰もいただいた。
当時の開発に携わった技術者のみなさんに振り返っていただいた。
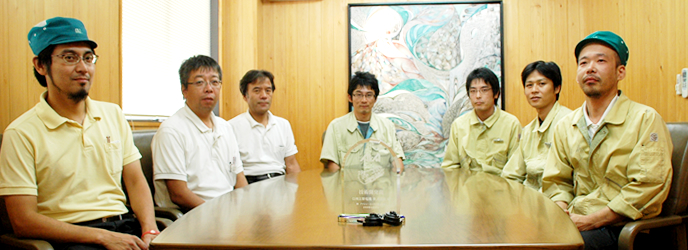
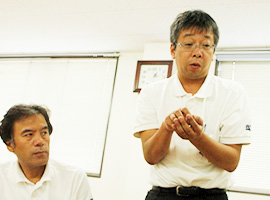

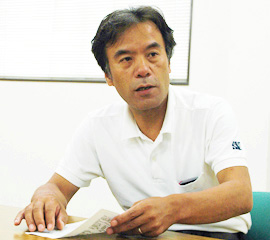
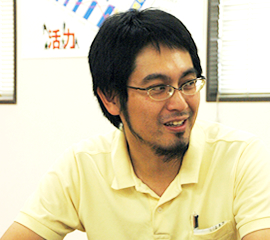
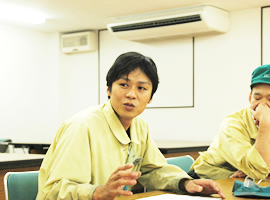
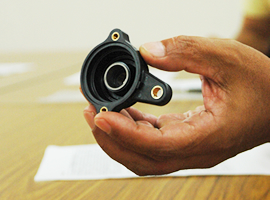
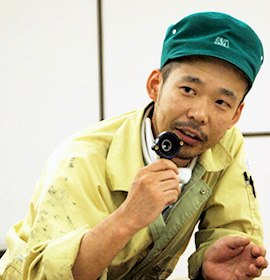

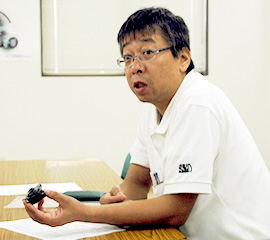
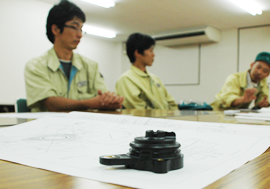
品質保証部門長M : 当初は弊社と取引のある樹脂材料の会社に相談があったらしく「信州吉野電機さんならなんとかなるんじゃないか?」ということで話をいただきました。
さっそく伺い、技術開発の背景を確認し、どんなところに使われ、どんな機能であるかなどを確認して樹脂で可能かどうかを置き換えていくわけです。これまでアルミダイキャストで製造されていた製品でしたので寸法公差など樹脂では無理な部分もありますから、まずは設計サイドの図面を検討しながら開発に入っていきました。
やはりアルミダイキャストから樹脂へという材質の変更が大きな問題だったわけですね。
自動車量産リーダーW : はい。でも先方にも構造上で譲れない部分がありますから、それを取り入れながら提案し、お客様に評価していただき、それから金型の設計に入るわけです。
金型部門長T : 車の部品というと非鉄金属が主流ですから先方にとっても、この部品が金属に替わるような樹脂化ができるかどうかというのは未知の世界だったと思います。当初はコスト的にナイロン素材という話もありましたが、ある程度強度が必要な部品でしたから、アルミに代わる樹脂ということで、素材の種類などもこちらから提案させていただきました。
自動車量産リーダーW : 苦労したのは「真円」を出すことでした。アルミダイキャストを切削して寸法出しする方法とは異なり、樹脂は収縮すると形状が変化し、真円がとれなくなってしまうのです。
この製品で求められることがそもそも樹脂でできるかどうかという大きな問題ですね。
金型設計主任M : そこで真円を出すために使ったのが金属との組み合わせでした。
われわれにはこれまでの蓄積や実績がありますから、すぐに樹脂と金属を組み合わせるインサート部品を使おうということになりました。あとは通常の金型と変わらないので、起こり得る問題を抽出し、金型で回避できる構造に作り込む試作を始めました。
なるほど。信州吉野電機の蓄積や実績が活かせたと。
金型部門長T : 金属と樹脂とを組み合わせるインサート技術は他部品で仕様した経験がありますから、それは容易に対応できました。
ところがまた問題が発生したのです。
インサート部品に強度を加えて使うと少々コストがかかることが分かり、再検討ということになったのです。しかし、そこでも、また過去の実績が生かされました。今度は金属の焼結という技術でした。インサート部品の色が違いますが、同じものを複数使うのではなく、1つは焼結という技術でのコストダウンを提案させていただきました。
金型設計主任M : 焼結ですと強度が上がりますし、自社で金型を作る技術も加わりますから量産性も上がると判断したわけです。
製品設計にいたるまでにもいくつもの問題を解決する必要があるんですね。設計からいよいよ実際の金型加工や生産に進むことでできていかがでしたか?
金型加工O : 使っていた樹脂はバリの出やすい性質だったので、どうしたら防げるだろうと考えたり、型彫り放電で苦労したり、フラットな金型を成型するとソリが出たり。1つ1つを設計へフィードバックしてクリアしながら作っていきました。
今思うと、設計段階で大変苦労していただいたので金型製造の加工では問題なくスムーズにいったと思います。
自動車量産リーダーW : 量産部門としてはガスが出て金型の合わせ目にバリが出やすいという特性を持っている樹脂でしたから、試作も大変でした。
しかも真円度を上げるためのカラー(金属部品)のセットには苦労しました。金属と樹脂では膨張率が異なりますから、円芯のズレが出てしまう。それを解消するために両方を油で温め、膨張させてからセットすることで精度を上げたのです。
金型設計の段階で金属の径を細くすれば簡単に解決できることなのですが、精度を保ちながら製造する事を考えるとそうはいかないと思い、ここでも過去の経験を生かしました。
金型加工O : 真円で円芯がズレないこと―ここは顧客の譲れない場所でもありました。モデリング(3D)してみると円や球面が接しているので、きれいな形に直す点ではとても苦労しました。しかし、これまでは与えられた仕事を形にしてきた中、今回は過去のノウハウから乗り越えたと思います。それでも補正は多かったですね。
金型部門長T : 裏面のフラットさを出すことには苦労しました。アルミダイキャストを切削して寸法を出す方法と違い、やはり樹脂だと収縮するため反りやすいんです。この部品の用途はゴムのOリングで封止して油漏れを防ぐ役割もあるため、必ずフラットでなければならない部分でした。
顧客から求められるポイントを実現しつついかに効率的な生産にするかが重要なのですね。こういう製品ですと部品検査としてもまたチャレンジがあったのではないでしょうか?
部品検査T : そうですね。中心がズレると補正を行って修正しますが、製品自体の公差が厳しく20~30カ所計らなくてはならなかったですから、真円に関してはマイクロメートル単位での微調整が何度も何度も続きました。
しかし、私にとっては入社し、配属されてすぐにこの立ち上げにかかわったので、とても思い出深い部品なのです。測定の仕方も知らない状態でしたから先輩方に教わりながら行い、来る日も来る日もこの製品だけを計測していた大変な日々を思い出します。
自動車量産リーダーW : そうやって問題点をクリアして量産に入った後は、焼結ブッシュに製造過程で付着する油が多いことを製造元で改善してもらったり、カラーの削りかすが多かったことを改善したりしました。
生産管理T : 初めての取引先となるので、生産管理部門としては梱包箱や納品の形態、ルートや納入方法などコストを含めて確認する必要があり、最善の方法を見つけるため、納品先の下見に出向きました。すると、自動倉庫に入れることが分かり、決まったサイズのパレットに乗せなければならないということが判明しました。これは現地確認したからこそ初めて分かったことだったのです。
初めての顧客で予想できないこともあり得るんですね。
品質保証部門長M : お客さまの手元に届くまでが我々の仕事ですからね。我々にとってはいつもと同じように普通に取り組んできたのですが、こうして、全社の力が結集した製品が「技術開発賞」という評価を受けたことはうれしかったですね。
先方も同じ技術者という立場でしたから生みの苦労を分かっていただけたのかもしれません。
金型設計主任M : これを機に多部品の展開につながればいいと思いますね。また機会があればチャレンジしたいと思っています。