- HOME
- スピードと品質で実現“精鮮部品”工程
- この製品はこうして生まれた vol.02
スピードと品質を支える生産工程
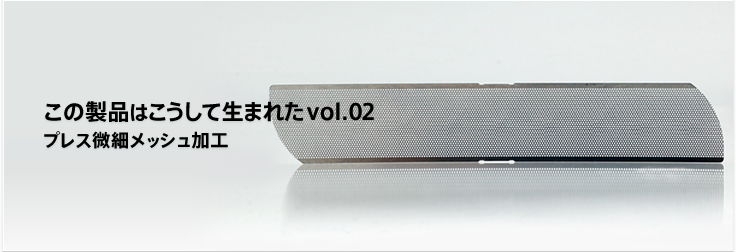
ある日、VA(生産・販売コストなどの低減)提案のひとつとして開発テーマに上がったのは「プレス微細メッシュ加工」。極薄のステンレス板に直径0.2ミリの穴を約6000穴開けるというものでした。
微細メッシュ、金型製作の経験には長けている信州吉野電機の技術者集団ですが、今回の場合、正攻法で金型製作をすれば金型だけで1000万円はコストがかかるというもの。しかし、なんの躊躇もなくチャレンジするのが、信州吉野電機の社員たる所以なのです。
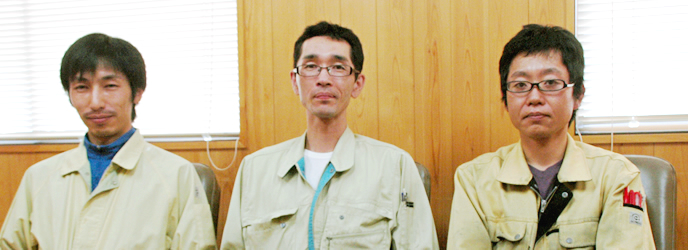
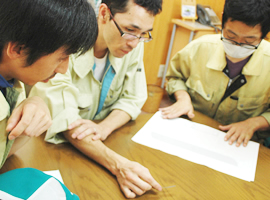
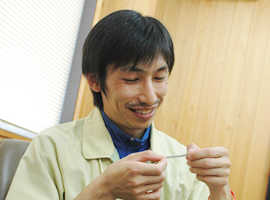
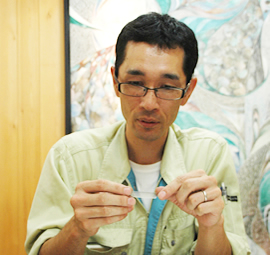
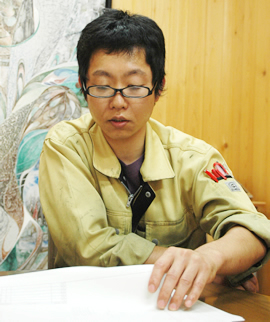
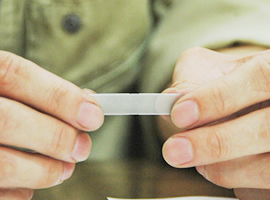
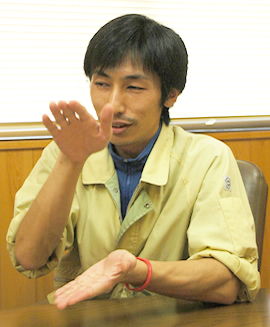
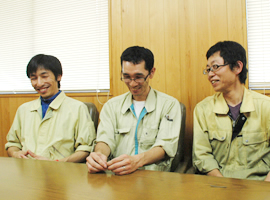
開発のきっかけは?
MS設計M : もともとエッチング方式だった製品をプレス加工でできないか‐という依頼から始まりました。エッチングは完全に穴を開けず、途中まで開けて最終的な穴は薬品で開けるという方式です。
私たちは、これまで直径0.15ミリというパンチの経験がありましたから、穴を開けることは出来ると思っていました。あとは果たして6000穴をどうやって開けるかというのが課題でした。
MS加工O : 今回はステンレスでしたが、今までにフィルム系の素材で250~300穴という製品は量産した経験がありましたから、そこから応用できました。
MS設計M : 6000穴を一気に開けるのは費用がかかるので‐1000万円くらいかかると言われていましたから。ならば今までの応用を生かして、4回のパンチ工程に分けて開けようということになりました。過去の経験があったので製品はできると思っていましたが、金型がどこまで持つのか‐という方が課題でした。
課題は出来るか出来ないかではなかったのですね。
MS量産N : 今まで経験したプリンターヘッド部品の技術がありましたから。出来ることは確信していました。
MS設計M : 以前は接着フィルムのように柔らかい素材でしたし、300穴くらいだと穴の間隔も広かったので、金型の素材についてもあまり考える必要がありませんでした。しかし、今回はステンレス。設計図の上では書けていても実際、金型の強度を含めて、加工ができるかどうかは未知数でした。
金型が細いものでしたから、もしかしたら1ショット目でいきなり金型が壊れる可能性もありました。だから極端なことを言えばこの金型で何ショットまでいけるのか?‐という挑戦でした。
製品が出てくるまでは緊張ですね。
MS加工O : そうでしたね。トライの時は、みんなで機械を囲んで、製品の出口1点に集中して見ていました。
MS設計M : 1ショットごとみんなでドキドキし、大丈夫かな?とのぞきこんでいた感じです。
MS量産N : プレスは従来と同じ作業なのですが、久しぶりの微細金型でしたし、1回目で金型が壊れる心配もあったので緊張しました。ですから初めは手動で行い、1ショット1ショット集中し、相当神経も使いました。
それでは1個目が無事に取れた時はうれしかったでしょうね。
MS設計M : 金型を作った後、こんな細かいものを組めるのか?‐ということも心配でした。金型は部品と部品の組み合わせですから、部品が1個ズレただけでも上型と下型が合わず、穴を開けるパンチが入らなくなる可能性もありましたからね。これだけ微細なものは造ったことがなかったので、最初の1個目を手にしたときにはうれしかったですね。
MS量産N : 正直ホッとしました。
いつものことですが、新しい金型のトライは慎重に、いつも以上に慎重にいきます。それに今回は穴径が小さいですし、数も違うのでものすごく緊張しました。
材料は自動で送らず、最初の製品が出来るまでは手動で少しずつ少しずつ金型を閉じ、上型と下型が合っていると分かった段階で一気に抜くという作業でした。1ショット目で金型を壊してしまう可能性もありましたから、1つ1つの工程を確認しながら金型を閉じ、最終工程まで丁寧に行いました。そして、1つ目の製品が出来上がったということは金型も全工程の動作ができるということ。うれしかったですね。
予想通りの製品が出来たんですね。
MS設計M : 最終的に外観で測定をして穴径、穴バリ問題なしという製品が完成しました。
MS加工O : 期待通りでした。
社内でも金型製造部門の技術が改めて評価されたようですね。
MS設計M : どちらかというとモールドが主な会社ですから、ここまで微細な穴をプレスで開ける技術があるということは社内でも知られていなかったのかもしれません。
商品化ではなく開発がテーマだったこの製品。実は、納期は約1カ月後の社長の誕生日だったそうですね。
良いプレゼントとなりましたね
MS加工O : 完成したのは誕生日でした。というか、どうしても間に合わせたかったですね。とにかく製品を作ることにエネルギーを費やしていたので余裕がなく、リボンはかけませんでしたが(笑)、”贈り物”ができて良かったです。
また1つ会社の強みができました。
MS設計M : どうやったらできるのか‐から始まり、苦労もありましたが製品になったので良かったと思います。
MS量産N : 当初のテーマ通り、難しい形状のものをプレス加工で対応できたことはうれしかったですね。今回の開発を機に、金型の精度や技術などプレス加工の凄さと面白さを改めて実感しました。
MS加工O : 今回のようにテーマを与えられることは多く、常に新しい可能性にチャレンジさせてもらえる環境はありがたく、とても良い経験となりました。